8 Common Problems And Solutions In Carton Printing
Carton Printing is an important part of the packaging industry, but various problems may be encountered during the printing process. Here are some common problems and solutions:
Problem 1: Poor color stacking effect In Carton Printing
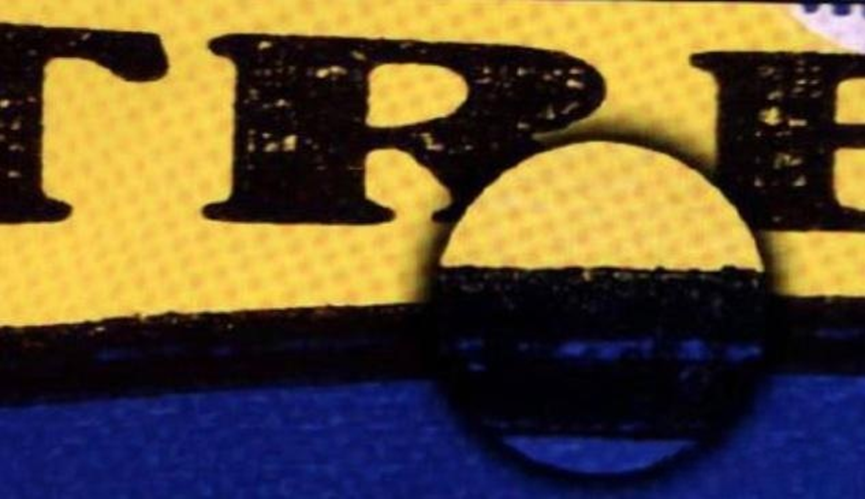
【Reason】
1. When printing the subsequent color in multi-color overprinting, the previous color is not yet dry;
2. The color printed later causes the previous color to peel off;
3. The post-printed colors cannot be overprinted.
【Solution】
1. Increase the drying speed of the first color;
2. Reduce the viscosity of post-printing ink or reduce printing pressure;
3. Reduce the viscosity of the latter color or improve its adhesion.
Problem 2: The print is stained during the carton printing process
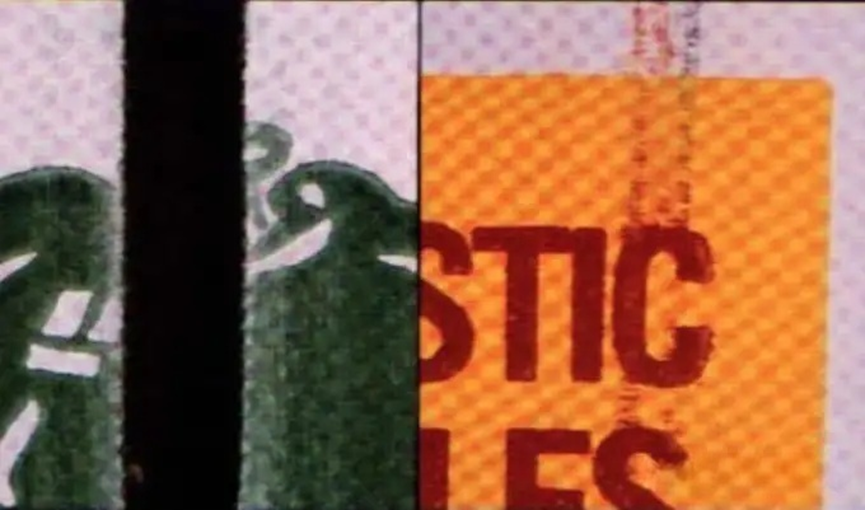
【Reason】
1. The ink does not dry or the ink film is too thick;
2. The bottom ink film layer is uneven;
3. Excessive surface tension makes ink difficult to dry.
【Solution】
1. Increase drying speed;
2. Measure and adjust the pressure between the anilox roller, printing plate and pressure roller, and the parallelism of the axis;
3. Replace the solvent, reduce the thickness of the ink film, or increase the drying capacity.
Problem 3: The printed matter is unclear
【Reason】
1. The printing plate pressure is too small;
2. The ink film layer is too thin;
3. Ink has high viscosity;
4. The cardboard surface is too wet or too shiny;
5. The pH value is too low.
【Solution】
1. Increase printing plate pressure;
2. Increase the thickness of the ink layer;
3. Add slow drying agent to lower the pH value of the ink, or increase the machine speed;
4. Add appropriate additives;
5. Check and adjust the pH of the ink to the appropriate value.
Problem 4: Printing ghosting
【Reason】
1. The ink has thick consistency and strong viscosity;
2. The printing plate is not tight or “the bottom pad is empty or solid”;
3. The printing pressure is adjusted too large;
4. The roller closing pressure is not working properly;
5. The paper teeth hold the paper with insufficient pressure;
6. The roller gear or bearing is worn and loose;
7. The drum lining is inappropriate.
【Solution】
1. Add appropriate additives to reduce the viscosity of the oil;
2. When the printing plate is tightened, tighten each screw gradually and evenly. Do not tighten one screw at once, so that the printing plate cannot fully and evenly adhere to the surface of the drum;
3. Appropriately reduce the pressure of the roller and reduce the expansion and contraction coefficient of the rubber cloth;
4. Recalibrate and adjust the clutch pressure mechanism and repair the worn parts to make the drum clutch pressure work accurate, coordinated and unified;
5. Technicians should check the teeth of the roller. If the gripping force is uneven or insufficient due to deformation, it should be re-adjusted (if the surface texture of the gripping teeth is worn and the paper edge is not tight, new accessories should be replaced);
6. Technicians should check the drum gear or bearing and repair the worn parts;
7. Technical personnel should re-measure the center distance of the drum, control the thickness of the lining according to the equipment specifications, and keep the linear speed of the drum consistent.
Problem 5: Printing burrs In Carton Printing
【Reason】
1. The drying time of ink is too fast;
2. The contact between the anilox roller and the layout is too large;
3. The facial paper has too much bad fiber and paper powder;
4. Poor quality of ink;
5. The pH quality of ink is improperly adjusted.
【Solution】
1. Speed up the machine appropriately or ask the ink dealer to help improve it;
2. Reduce the contact pressure between the pattern roller and the plate;
3. Wrap double-sided tape on the surface of the paper roller and apply powder on it to help remove paper powder from the flat surface;
4. Require suppliers to improve the quality of ink;
5. Adjust the pH value of the ink (8.5-9.5).
Problem 6: Uneven printing color In Carton Printing
【Reason】
1. Ink: The leveling property of ink is low;
2. If the lock plate is not locked tightly, it will also cause uneven color;
3. Bearings, gears, etc. vibrate.
【Solution】
1. Add leveling agent to the ink to deal with the problem of color unevenness;
2. Technicians should check whether the plate lock is too loose and tight it;
3. The technicians will solve the problem by repairing and replacing the carton printing machine.
Problem 7: The printing color is light
【Reason】
1. Too much water is added to the ink or the washing water is not drained;
2. The anilox roller is worn or dirty;
3. The viscosity of the ink is too low;
4. The thickness of the ink film is too thin;
5. Incorrect plate pressure;
6. Insufficient ink colorant.
【Solution】
1. a) Replace the ink or add fresh ink;
b) Check and repair drainage pipes and drying systems;
c) Measure and control the amount of water added in ink;
2. Clean or replace the anilox roller if necessary;
3. Increase the viscosity of the ink by adding fresh ink;
4. Increase the thickness of the ink film layer:
a) Increase the viscosity of ink;
b) Reduce ink scraping by the anilox roller;
c) Gradually increase the ink supply volume of the anilox roller;
d) Add more transfer agents to the ink formula;
5. Adjust the pressure between the printing plate and the printing material;
6. Ask the ink supplier to adjust the ink formula according to the characteristics of the machine.
Question 8: Ink bubbles In Carton Printing
【Reason】
1. Too much air is dissolved into the ink;
2. The air pressure of the ink pump is too high, causing bubbles or splashing;
3. The ink is excessively agitated, causing it to become wet and breathable;
4. There is a gap in the scraper blade;
5. Too much water is added to the ink;
6. The viscosity of the ink is too high;
7. The ink formula is wrong.
【Solution】
1. Check the sealing gasket and pipeline at the suction end of the ink pump, and repair if necessary;
2. Adjust the pump pressure to the minimum;
3. Reduce the speed of the pump or agitator to the minimum necessary amount so that the return line of ink is submerged;
4. a) Replace the doctor blade frequently;
b) Adjust the doctor blade angle and seal the ink tank;
c) Adjust the pump volume to keep the ink tank full;
5. Add fresh ink to increase the viscosity of the ink;
6. Reduce viscosity and eliminate foam;
7. Contact the ink supplier.