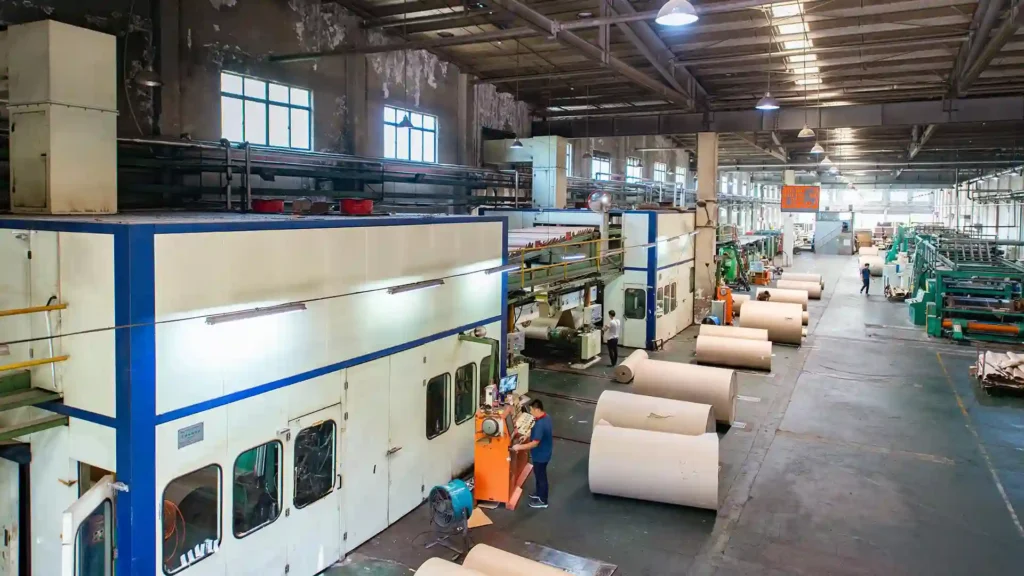
Proven High-Efficiency Double-Facer Solutions for Over 300 Packaging Enterprises Worldwide
I. Why Does the “Heart” of Corrugated Board Production, the Double-Facer, Keep Malfunctioning?
In a corrugated board production line, the double-facer plays a pivotal role as the “bonding core”. It laminates single-faced corrugated paper with linerboard into three-ply or five-ply boards, directly determining the bonding strength, flatness, and production efficiency of the boards. However, in actual production, it often becomes a “high-risk area” due to environmental factors, raw materials, and operational issues:
▶ Three Typical Pain Points
Environmental Challenges | Common Problems | Hidden Costs |
Humid Regions | Corrosion of corrugating rolls, water accumulation on heating plates, poor bonding | 30%+ increase in annual maintenance costs |
Recycled Paper Processing | Paper jams, 12%-15% scrap rate, high energy consumption | 20-30 increase in cost per ton of board |
Cold/High-Dust Areas | Difficult equipment startup, rapid component wear, frequent maintenance | Over 500 hours of annual downtime |
Data Source: 2024 Global Packaging Equipment Industry White Paper
II. How to Keep the Double-Facer from “Rusting and Malfunctioning” in Humid Environments?
Pain Point: In regions like Southeast Asia and South Asia with humidity exceeding 80%, traditional double-facers often experience corrosion of corrugating rolls and gearbox jams within 1-2 years of use, resulting in a 15% poor bonding rate and over 20 maintenance incidents annually.
▶ Intelligent Moisture-Proof and Rust-Resistant Solutions
🛡️ Full Stainless Steel Upgrade + Nano-Coating Protection
Key components are made of food-grade 304 stainless steel with nano moisture-proof coating, offering over 1,000 hours of salt spray test resistance (compared to only 300 hours for ordinary carbon steel). This extends the service life to 8-10 years in humid conditions, eliminating bonding failures caused by rust from the source.
🌡️ Wide-Temperature Intelligent Temperature Control System
Integrated with temperature sensors and dynamic heating compensation technology, it supports stable operation in a wide temperature range from -20°C to 50°C. Even with a 30°C day-night temperature difference, it can automatically adjust the heating plate temperature (accuracy ±1°C), preventing local delamination of the board due to temperature fluctuations.
💧 Intelligent Automatic Drainage System
The heating plate section is equipped with high-precision drain valves that continuously monitor and automatically discharge condensate levels. Combined with the flow channel design, it reduces the probability of water accumulation on the heating plate by 90%, completely solving the problem of board sticking in humid environments.
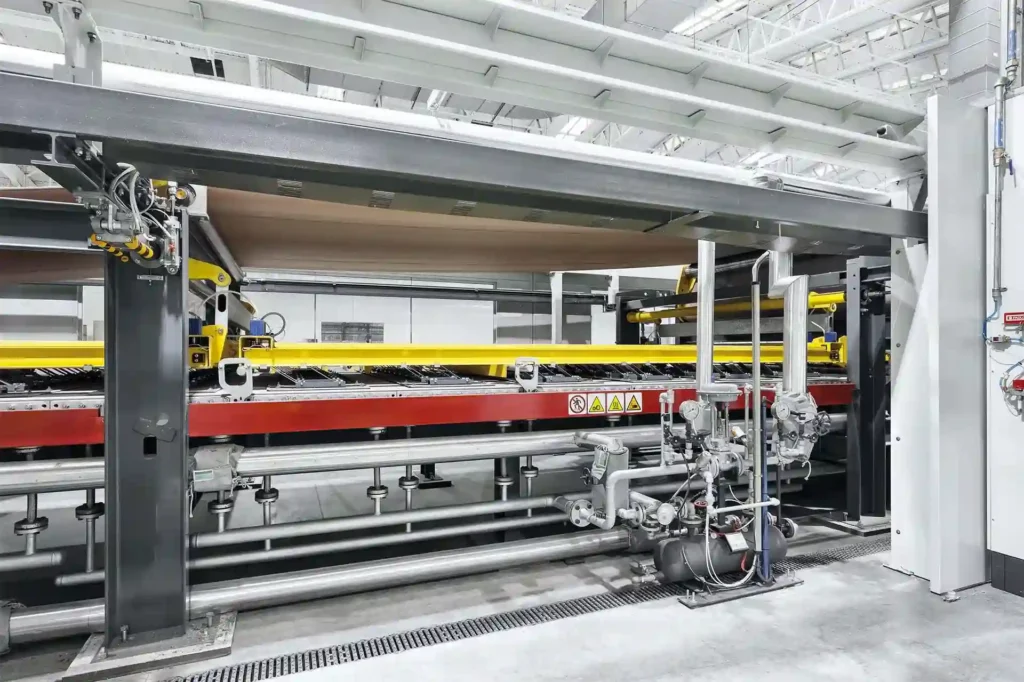
III. Struggling with Recycled Paper Processing? Here’s How to Cut the Scrap Rate by 12%
Industry Challenge: When processing recycled paper (with 12%-15% moisture content) or low-basis-weight base paper, equipment often experiences paper jams due to poor paper toughness and uneven thickness. The scrap rate typically reaches 12%-15%, especially in markets like South America and the Middle East, where the usage of recycled paper exceeds 60%.
▶ Intelligent All-Paper Adaptation Solutions
🎚️ Dual-Pressure Intelligent Adjustment Technology
Through servo motors, it dynamically adjusts the pressing pressure (accuracy ±0.1MPa), supporting self-adaptation for board thicknesses from 0.5mm to 2.0mm. It can stably process recycled paper with up to 18% moisture content, solving issues like local crushing or insufficient bonding caused by uneven paper thickness.
🕶️ AI Vision Alignment and Tension Control System
Equipped with high-speed vision detection modules, it captures paper deviation in real-time (accuracy ±0.5mm) and automatically calibrates in conjunction with the tension control system, reducing the paper jam frequency from 5 times per hour to less than 0.5 times, significantly enhancing the continuity of recycled paper processing.
🌿 High-Efficiency Heat Recovery Technology
The steam heating system boasts a thermal efficiency of over 90%. The supporting waste heat recovery device reuses exhaust heat, reducing energy consumption by 25% compared to traditional models. This saves 15-20 in processing costs per ton of recycled paper, perfectly suiting low-cost production requirements.
IV. Facing Strict Policies and Logistics Hurdles? How to Ensure Smooth Customs Clearance and Stable Operation of Double-Facers?
Reality Check: Requirements like SASO certification in the Middle East, GOST certification in Russia, and port congestion in South America can delay equipment customs clearance by 30-60 days. Language barriers and difficulties in obtaining spare parts often lead to a failure response time of over 72 hours during the initial operation phase.
▶ Globalized Compliance and Convenient Service Solutions
📦 Modular Design + Certification Assistance Support
The equipment features a detachable modular structure (6 core modules, each weighing ≤20 tons), reducing transportation volume by 40% and easily adapting to sea freight or China-Europe Railway Express. Our team can assist customers in preparing materials for GOST, SASO, CE, and other certifications, providing process guidance to shorten the customs clearance cycle.
🌐 Multilingual Intelligent Operation + Remote Diagnosis System
The operation interface supports 12 languages, including English, Russian, and Arabic, accompanied by video training tutorials, enabling users to master basic operations within 2 hours. The cloud-based diagnosis system collects equipment data in real-time, resolving 90% of common faults online 24/7, reducing dependence on local technicians.
💳 Flexible Settlement and Regional Spare Parts Response
Supports multi-currency settlement in RMB, Ruble, US Dollar, etc., and offers customized payment plans according to customer needs. Through cooperation with regional partners, it enables rapid allocation of commonly used spare parts, shortening the delivery cycle and reducing downtime.
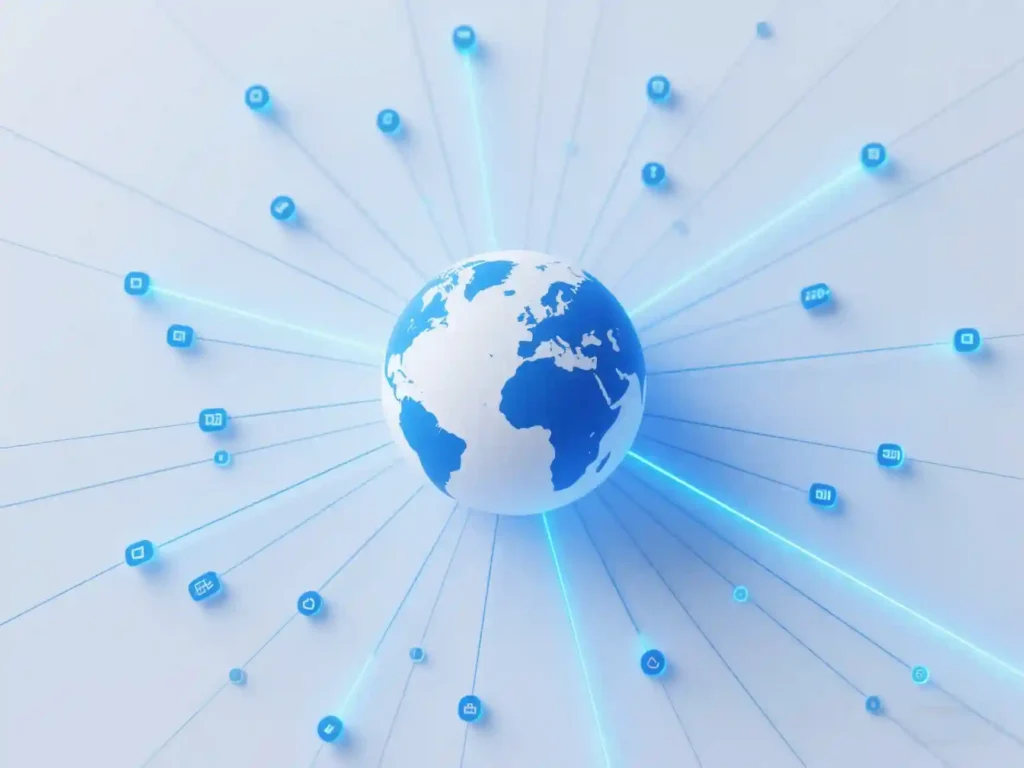
V. New-Generation Double-Facers: Revolutionizing Production with 4 Core Technologies
🤖 1. Intelligent Pressing System: Double Leap in Precision and Efficiency
- The floating heating plate adopts an airbag suspension technology, automatically compensating for equipment vibration and thermal deformation. The flatness error of the board is ≤0.5mm, and the bonding strength increases to 1.8N/m (industry standard 1.5N/m).
- It can store 100 sets of process parameters with one click, reducing the order changeover time from 10 minutes to 3 minutes and increasing the production efficiency of small-batch orders by 50%.
⚡ 2. Energy-Saving and Efficiency-Enhancing Technology: 30% Electricity Savings, Environmentally Friendly
- The servo motor drive system saves 30%-40% more electricity than traditional models, meeting strict energy efficiency standards such as EU ErP and Middle East GCC.
- Optional exhaust gas purification devices are available, with VOC emissions below 100mg/m³, satisfying global mainstream environmental certification requirements.
⚙️ 3. Durable Design: Tripling the Lifespan of Core Components
- The corrugating rolls are processed by vacuum quenching, with a surface hardness of HRC58-62 and a wear-resistant lifespan of over 10 years.
- The upgraded bearing sealing structure extends the maintenance cycle from 500 hours to 2000 hours in dusty environments, reducing downtime for maintenance.
🚨 4. Intelligent Early Warning System: Predicting Faults 72 Hours in Advance
Through IoT sensors, it monitors equipment operation data in real-time. The AI algorithm analyzes parameters such as vibration, temperature, and pressure, enabling 72-hour advance warning of potential faults like bearing wear and heating anomalies, reducing unplanned downtime risks by 60%.
VI. Exclusive Adaptation Solutions for Your Factory, Wherever It Is
🌴 1. Humid and Rainy Regions (e.g., Southeast Asia, Africa)
- Moisture-Proof and Rust-Resistant: Full stainless steel body with Teflon coating, combined with an intelligent automatic drainage system.
- Recycled Paper-Friendly: Standard dual-pressure intelligent adjustment technology for efficiently processing local high-moisture-content raw materials.
❄️ 2. Cold/High-Dust Regions (e.g., Central Asia, Middle East)
- Wide-Temperature Operation: Stable startup in -20°C to 50°C environments, with a gearbox heating jacket preventing lubricating oil from freezing.
- Dust-Proof Design: Labyrinth seal for bearings and regular blowing system to reduce dust damage to mechanical components.
🌍 3. Multilingual/Logistics-Challenged Regions (e.g., South America, Eastern Europe)
- Worry-Free Operation: Localized language operation interface and video training tutorials for quick mastery within 2 hours.
- Convenient Transportation: Modular design, each module ≤20 tons, adaptable to global mainstream transportation methods.
VII. How Companies Achieved “Cost Reduction and Efficiency Improvement” with Our Double-Facers
✅ Case 1: An E-commerce Packaging Factory in Indonesia
- Pain Point: 15% monthly scrap rate due to humid environment and recycled paper, with annual losses exceeding $300,000.
- Solution: Moisture-proof double-facer (stainless steel + intelligent drainage) + all-paper adaptation technology.
- Result: Scrap rate reduced to 3%, production capacity increased by 20%, and equipment cost recovered within 12 months.
✅ Case 2: A Russian Industrial Packaging Group
- Pain Point: Frequent winter downtime, with maintenance costs accounting for 18% of production costs.
- Solution: Wide-temperature double-facer (-20°C temperature control system) + remote diagnosis system.
- Result: Continuous production at -20°C achieved, 故障 response time reduced from 48 hours to 4 hours, and annual maintenance costs decreased by 60%.
VIII. Unlock Your Exclusive Solution Now
📩 1. Free Access to “Double-Facer Selection Technical Guide”
Click Contact Us to obtain:
- Equipment configuration suggestions for different climatic/raw material scenarios.
- Certification process guidance and tariff optimization strategies for major global markets.
- Energy efficiency comparison analysis of over 300 enterprises (including ROI calculation).
🔧 2. Apply for a Free Production Line Diagnosis
Provided by a team of engineers with 10+ years of experience:
- Comprehensive inspection of existing equipment issues (bonding strength, energy consumption, failure rate, etc.).
- Customized solutions with detailed technical parameters and cost analysis.
🛎️ 3. Worry-Free After-Sales Service: Keeping You at Ease
- Extended Warranty for Core Components: Leading industry warranty service for core components, with specific terms subject to contract agreements.
- 24/7 Global Response: Multilingual service teams available online around the clock, combining remote guidance and local collaboration to resolve technical issues promptly.
IX. Disclaimer
The technical parameters and case data in this article are for typical application reference only. The actual product configuration and service details are subject to the contract. Equipment performance is affected by factors such as raw material quality and operating environment. Please contact us for a one-on-one solution.
Choosing the right double-facer means more stable production, lower costs, and higher profits. Contact us now and let our professional team customize an adaptation plan for you. Say goodbye to production pain points and embark on a journey of high-efficiency packaging!
🌐 Visit our website: [jeytop.com]
🔗 Follow on LinkedIn: [Yong Lee—Jeytop Carton Machinery]
📧 Email: [jeytopmachinery@163.com]
📱 WhatsApp:[86-15230792110]