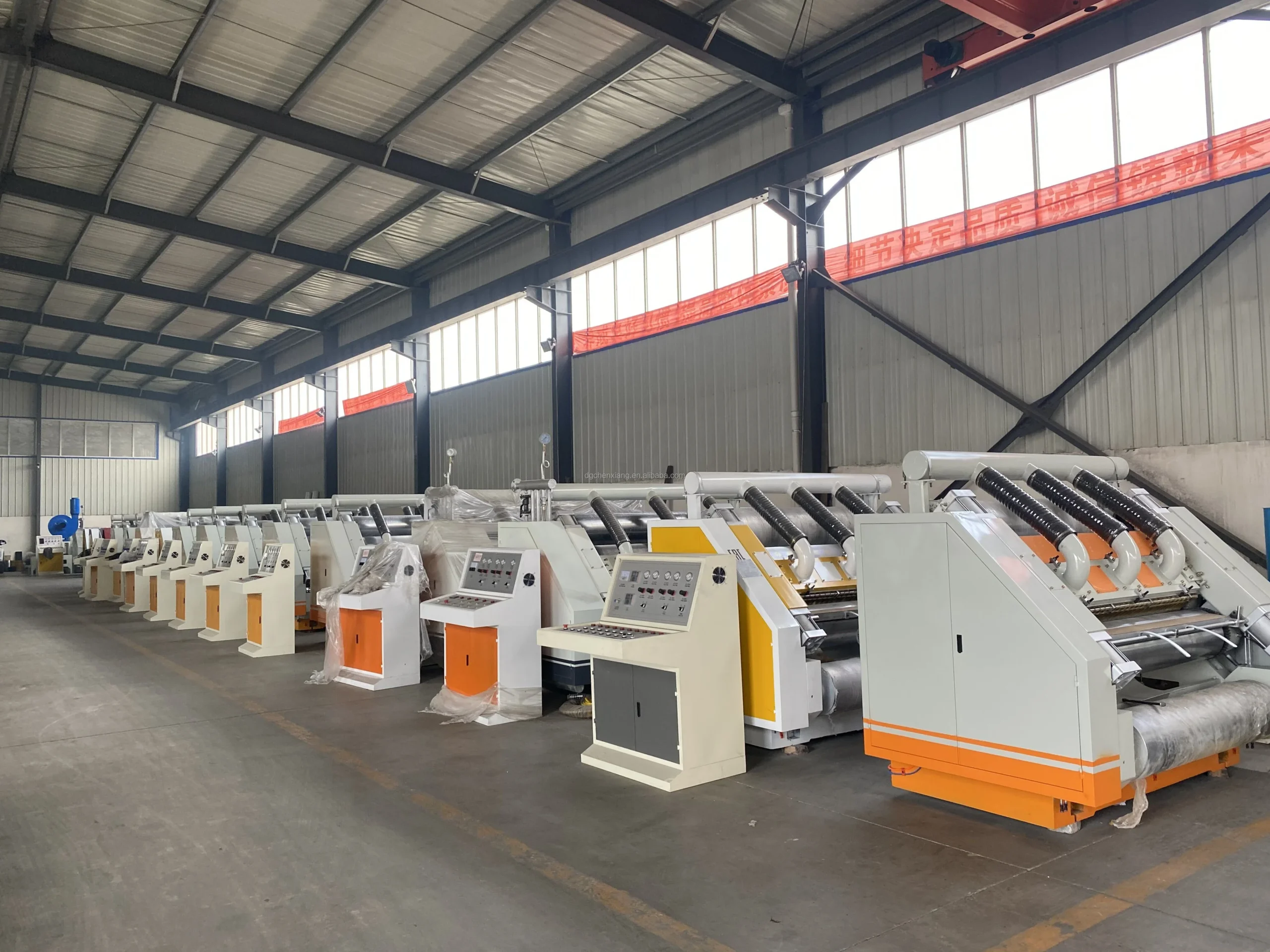
The single facer corrugation machine is the core of corrugated board production. It is responsible for producing the corrugated layer required for each carton and plays a vital role in the corrugated packaging industry. Choosing a suitable single-face corrugator can significantly improve production efficiency and cardboard quality.
What Is a Single Facer Corrugated Machine?
A single facer machine combines a corrugated medium and liner paper using heat, pressure, and adhesive to form single-faced corrugated board — the base for most packaging boxes.

It streamlines the corrugation process and ensures consistent production of durable packaging materials.
How Does a Single Facer Work?
Single facer machines form flutes from kraft paper and bond them with liner paper. Here’s how:
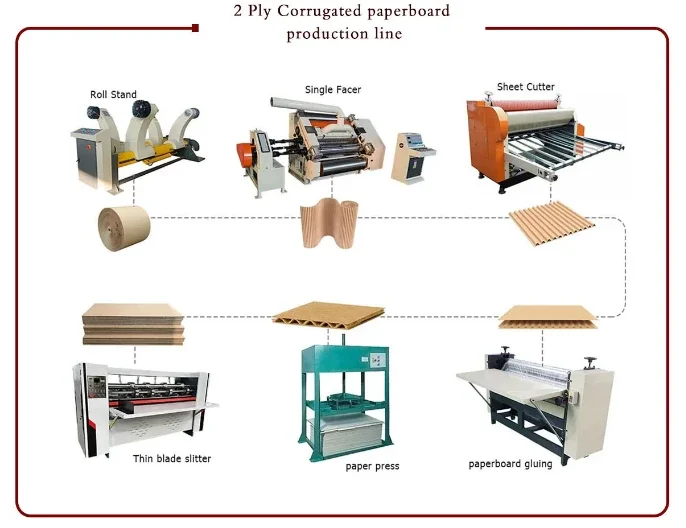
Key Steps in Operation
- Raw Material Feeding: Kraft paper rolls serve as fluting and liner paper.
- Corrugation Formation: Heated rolls shape the fluting medium.
- Adhesive Application: Glue is applied to flute tips.
- Bonding and Heating: Liner is bonded to the flutes with heat.
Process Step | Function | Output |
---|---|---|
Raw Material Feeding | Supplies kraft paper | Paper rolls |
Corrugation Formation | Forms flutes in the medium | Corrugated medium |
Adhesive Application | Applies glue | Prepared medium |
Bonding and Heating | Bonds liner and flute with heat | Single-faced board |
What Types of Single Facer Machines Are There?
- Cassette Type
Designed for fast flute change, this modular machine allows quick replacement of corrugating rolls in under 10 minutes. Ideal for production lines requiring frequent flute profile changes. - Standard Type
Traditional fixed-roll configuration, suitable for stable, continuous production. Based on structural layout, it includes:- Inclined Type
Features a tilted frame design, improving operator access and paper feeding angle. Common in compact production environments.
Example: SF280 Fingerless Single Facer - Fixed Type
Horizontal structure with a rigid chassis, designed for high stability during long-run production. Easy to maintain and operate under consistent settings.
- Inclined Type
Why Are Single Facer Machines Important?
They are essential for producing high-volume corrugated packaging, reducing labor and improving board quality.
Key Benefits
- Efficiency: Up to 350m/min high-speed production
- Durability: Strong bonding ensures board strength
- Versatility: Supports various flute profiles (A, B, C, etc.)
- Eco-Friendly: Works with recyclable materials
Key Components of a Single Facer
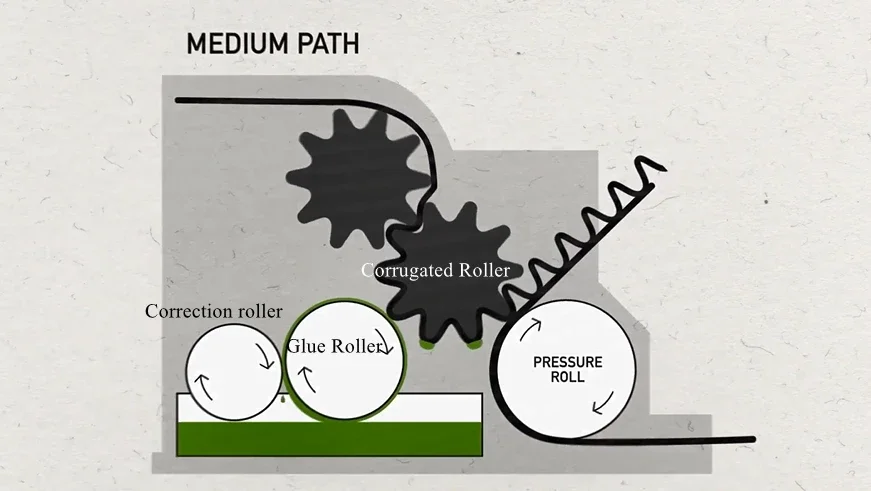
Understanding each part helps in maintenance and efficient operation.
- Corrugating Rolls: Shapes paper into flutes
- Pressure Rolls: Press liner onto flute tips
- Glue Unit: Applies precise glue lines
- Heating System: Heats paper and glue for bonding
Component | Function |
---|---|
Corrugating Rolls | Forms the fluted shape |
Pressure Rolls | Bonds flute tips and liner |
Glue Unit | Applies adhesive |
Heating System | Ensures strong adhesion |
Production Capacity & Applications
Typical capacity: 60–350 m/min. Ideal for medium to big manufacturers.
Applications:
- Single or double-wall corrugated cardboard
- Box liners
- Lightweight packaging solutions
Common Problems and Solutions
- Flute Misformation → Check roll wear and pressure settings
- Delamination → Inspect glue temperature and pressure
- Uneven feeding → Align paper rolls and correct tension
How to Maintain a Single Facer Corrugation Machine
- Daily cleaning of dust and glue residue
- Lubricate moving parts and check roll temperatures
- Monthly alignment check for bearings and gears
- Replace worn corrugating rolls when needed
How to Choose the Right Machine
- Required speed and output volume
- Desired flute profile (A/B/C/E/F)
- Heating method (steam/oil/electric)
- Ease of maintenance and part replacement
- After-sales service & spare parts availability
Single Facer Machine Price Range
Typically $20,000 to $120,000 depending on:
- Automation level
- Corrugating roll change system
- Speed and width
- Heating system type
FAQs
What is a single facer machine used for?
To produce single-faced corrugated board, the base layer for most packaging boxes.
What flute types can be produced?
A, B, C, E, F – depending on machine roll type.
How fast does it operate?
60–350 meters per minute, depending on the model.
How long does roll change take?
Cassette type machines can change rolls in under 10 minutes.
Looking for a reliable single facer supplier? Contact Jeytop for high-performance machines with global support and expert service.