From Inception to Leading Manufacturer
Discover how Jeytop has grown and evolved over the years in the carton machinery industry.
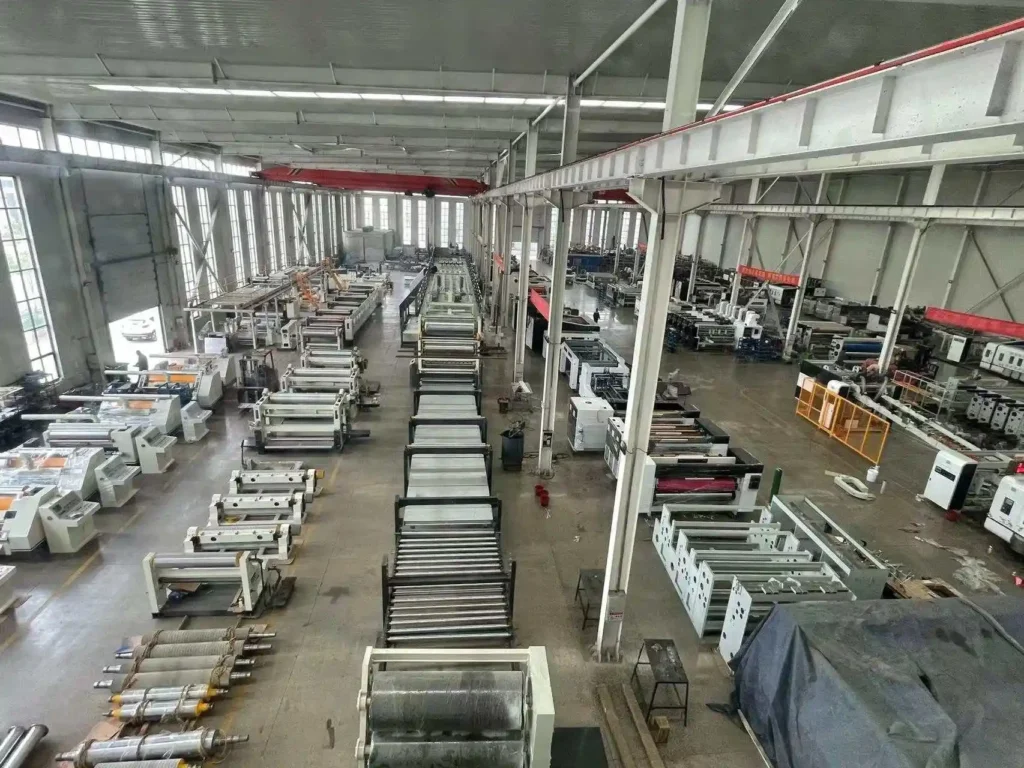
Foundation and Vision in year 2010
Jeytop was founded with a vision to revolutionize the carton machinery industry through innovation.
Early Success and Growth in year 2013
Through dedication and quality products, Jeytop quickly expanded its client base in various regions.
Global Expansion in year 2019
Jeytop has successfully exported machines to 30+ countries, enhancing our global footprint.
Commitment to Excellence in year 2023
Our focus on quality and customer service has solidified our reputation as a trusted leader.
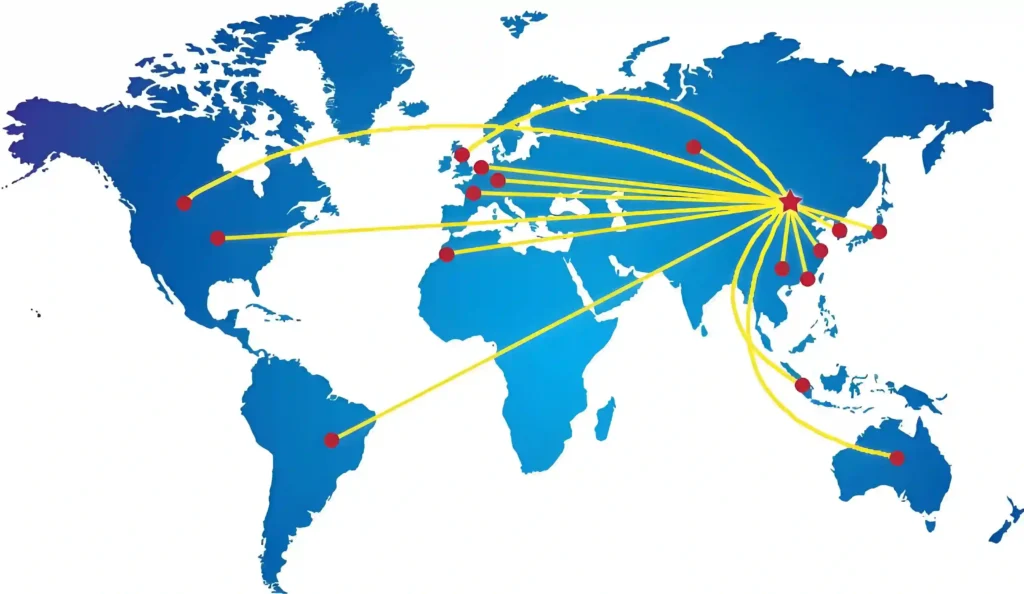
- 24/7 Worldwide Response: Dedicated team ensures prompt replies to inquiries, quotes, and technical consultations within 24 hours.
- Tailored Solutions: We design and engineer machines to meet specific requirements, including size, speed, material compatibility, and automation levels. Leverage our OEM/ODM capabilities for turnkey solutions.
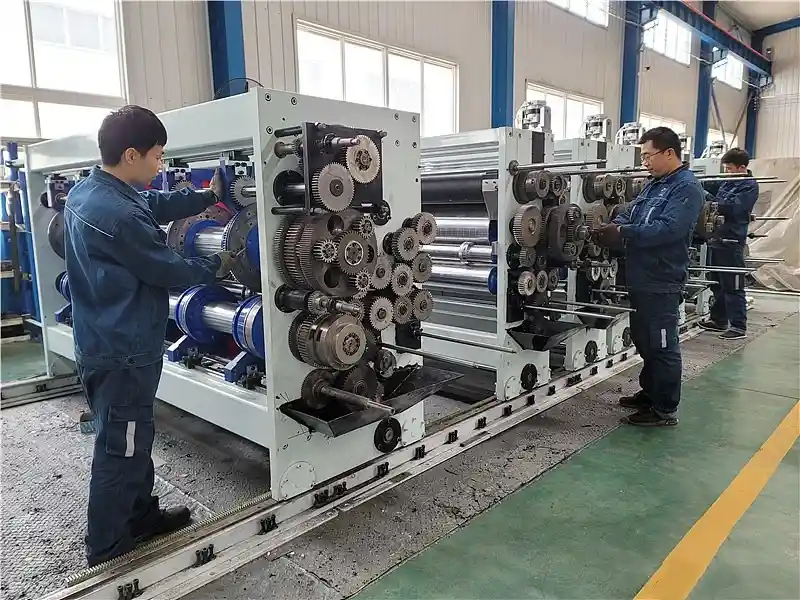
- Warranty Coverage: Free replacement of defective parts during the warranty period (terms apply).
- Cost-Effective Spare Parts: Post-warranty replacements available at factory-direct prices, with global shipping.
- Priority Service: Dedicated support line for urgent spare part requests and technical assistance.
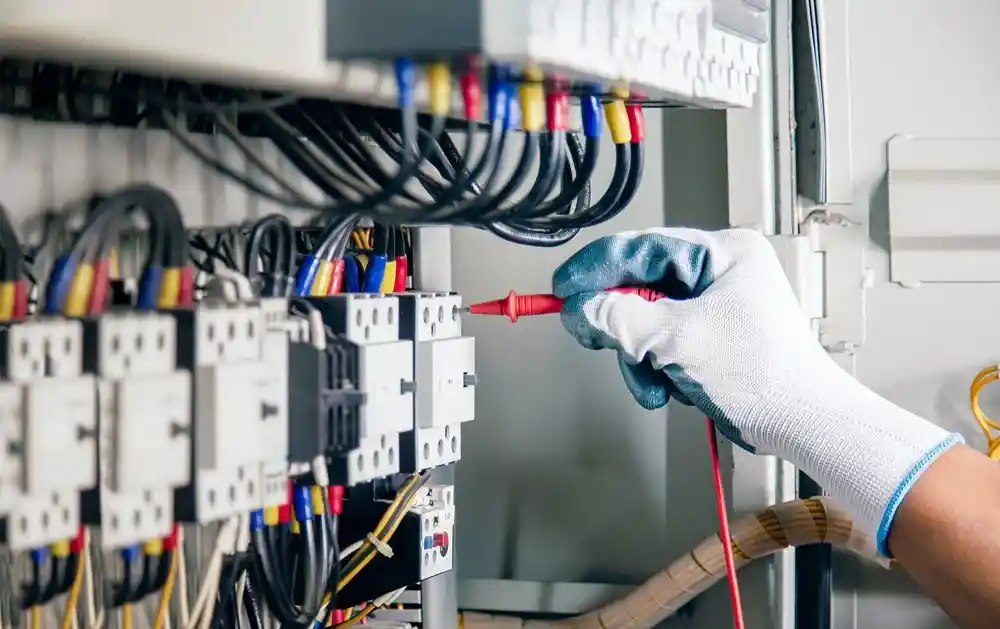
- Onsite Support: Certified technicians provide full installation, start-up, and calibration for machines worldwide.
- Repair Services: Swift troubleshooting and repairs for all models, with availability for urgent overseas requests.
- Preventive Maintenance: Proactive maintenance plans to optimize machine performance and extend lifespan.

- Comprehensive Programs: Hands-on training sessions for operators and maintenance staff, covering safe operation, troubleshooting, and basic repairs.
- E-Learning Resources: Supplementary online guides and video tutorials for continuous skill development.
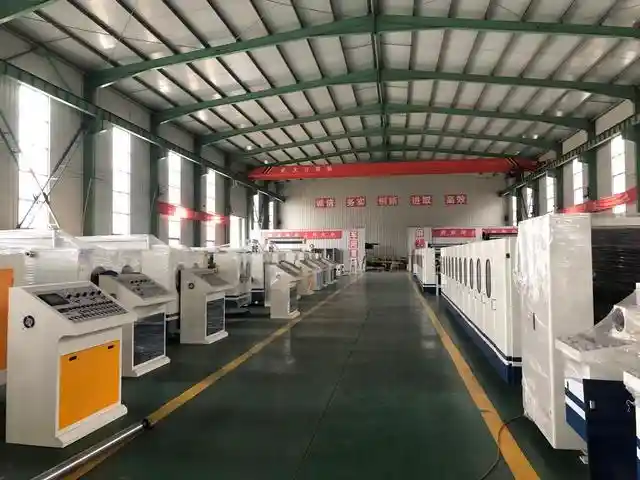
Direct Factory Advantages
As the original equipment manufacturer, we ensure full control over:
- Quality consistency: ISO-certified production protocols
- Cost efficiency: No middleman margins, with volume-based discounts
- Delivery precision: In-house scheduling for on-time fulfillment
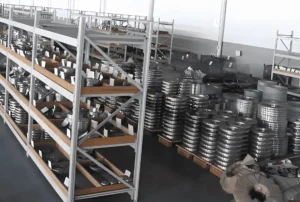
Premium Material Selection
Built to endure industrial demands using:
- High-grade steel: Domestically sourced HRC 50-55 alloy frames
- Global electrical systems: Siemens/Omron/Schneider components
- Precision bearings: NSK/INA-branded transmission modules

Multi-Stage Quality Verification
Rigorous inspection processes guarantee reliability:
- Raw material certification (Mill Test Reports)
- Assembly-phase dimensional accuracy checks
- 72-hour continuous operational stress tests pre-shipment
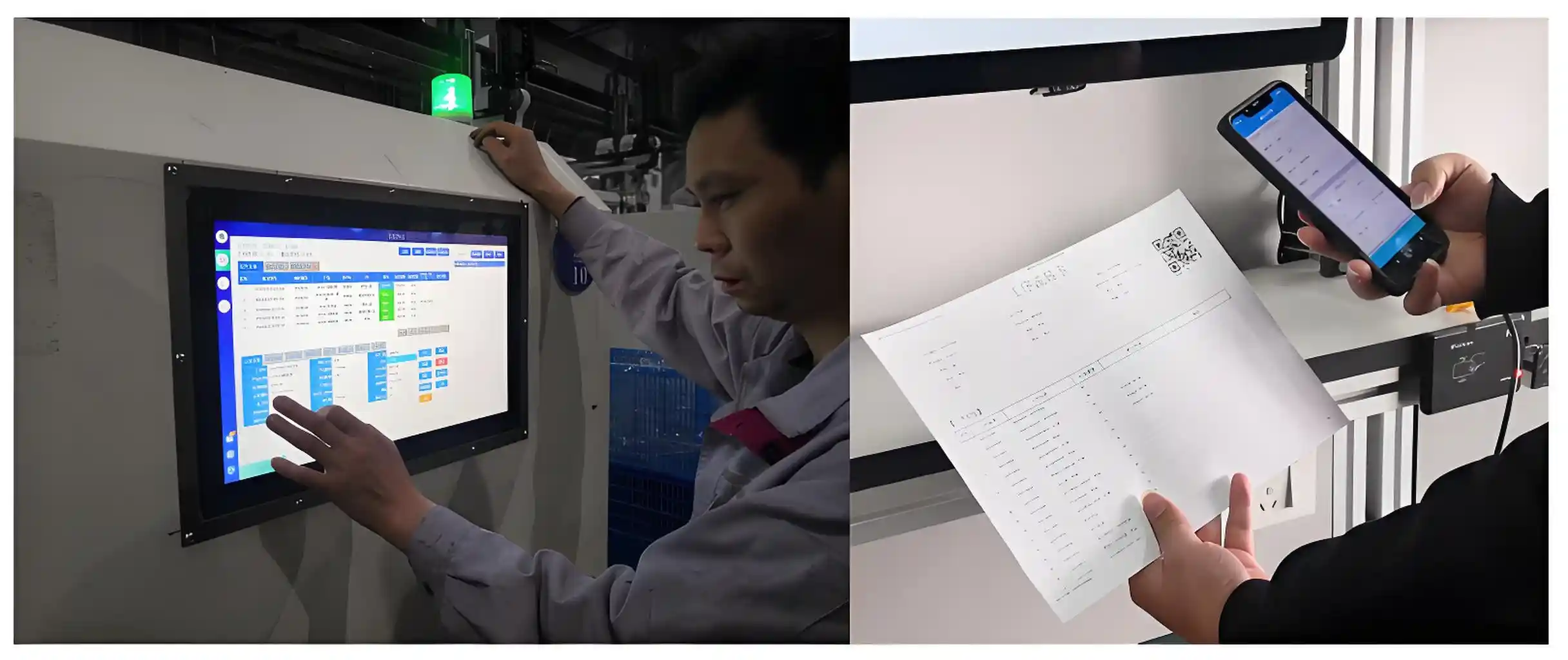
Agile Order Execution System
Streamlined workflows for predictable outcomes:
- Real-time production progress dashboard access
- Dual-component sourcing to prevent delays
- EXW/FOB/CFR/CIF shipping flexibility
- 30,000㎡ warehouse with strategic buffer stocks
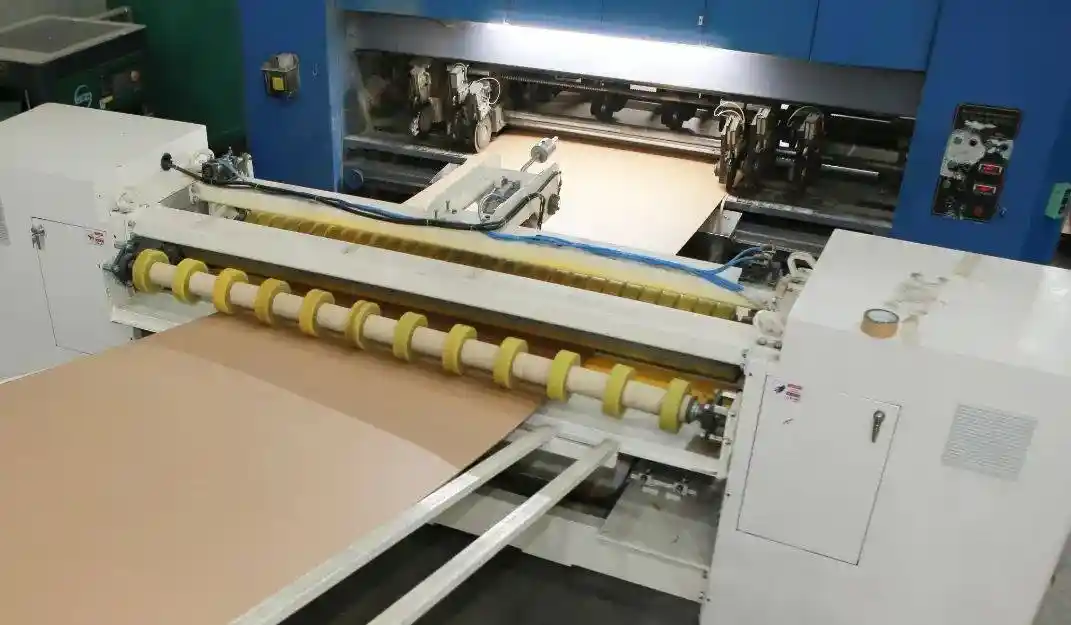
Upgrade-Ready Engineering
Machinery designed for evolving needs:
- Modular architecture for future retrofits
- Energy-saving configurations (CE-certified drives)
- Scrap reduction technology (<1.5% material waste)

Certified quality assurance
Globally recognized compliance and transparency:
- ISO certified production system (ISO 9001/14001)
- Third-party testing acceptance by independent inspection agencies
- Machine quality traceability documentation to ensure full accountability
Moments with Clients
Frequently Asked Questions
Find answers to commonly asked questions about our products and services.